Optimizing Conveyor Systems for Aggregate Handling
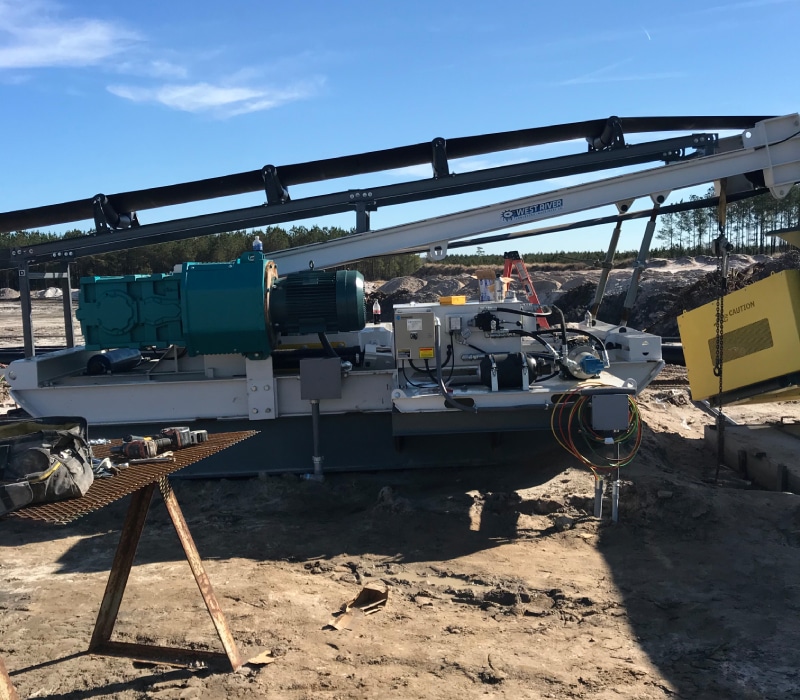
Conveyor systems are the lifeline of aggregate operations, keeping crushed stone, sand, and gravel moving efficiently through processing plants, storage yards, and onto transportation vehicles. However, the demanding nature of these environments, characterized by jagged material, fluctuating terrain, and high throughput, means achieving peak performance takes more than just installing a conveyor and walking away.
To minimize downtime, reduce operating costs, and extend equipment life, it’s essential to actively improve how these bulk material handling systems function. That includes addressing not just wear and tear, but flow control, alignment, dust suppression, and more.
Whether you’re managing a fixed plant or a mobile operation, fine-tuning system performance can lead to measurable improvements in safety, throughput, and maintenance intervals.
KEY FACTORS TO OPTIMIZE AGGREGATE CONVEYOR PERFORMANCE
To get the most out of your equipment, it’s important to take a strategic, system-wide approach. Improving performance begins with a handful of core factors—each one playing a critical role in boosting efficiency, minimizing downtime, and extending the life of your conveyor system.
BELT SPEED AND MATERIAL FLOW RATE
Belt speed directly affects throughput, energy use, and material spillage. If the belt moves too fast, material may bounce or segregate, especially with coarse aggregate. Too slow, and you sacrifice efficiency.
Optimizing the belt speed for the specific type and volume of material ensures smoother flow, reduced wear on components, and minimized carryback. It also reduces power consumption and the risk of slippage, especially in belt conveyors, which depend on consistent loading and speed to operate efficiently.
COMPONENT SELECTION AND WEAR RESISTANCE
Aggregate is unforgiving. Sand is highly abrasive. Crushed stone can cause impact damage. That means your system’s components—belts, pulleys, idlers, bearings—must be built for durability.
Opt for heavy-duty, abrasion-resistant materials and properly sized components. For example:
- Rubber belts with high tensile strength are ideal for sand and gravel.
- CEMA D or E idlers offer extended life in heavy-load applications.
- Properly sealed bearings keep contaminants out, reducing premature failure.
The right component choices also depend on the type of materials being moved—fine sand requires different specs than coarse, jagged rock.
If your operation uses overland conveyors or transfer conveyors, it’s fundamental to select components reinforced for long distances, heavy loads, and frequent directional changes.
Selecting components specifically for aggregate use reduces wear, extends equipment life, and lowers total cost of ownership.
DUST SUPPRESSION AND CONTAINMENT
Dust isn’t just a nuisance—it’s a safety and environmental concern. Poor dust control can impair visibility, trigger regulatory penalties, and accelerate equipment degradation.
Solutions include:
- Skirtboard sealing systems to prevent dust escape at loading zones.
- Enclosed transfer points to control fugitive dust.
- Water spray systems or foggers to suppress dust at the source.
A well-designed dust containment system reduces the risk of equipment failure, regulatory violations, and long-term worker exposure.
MAINTENANCE SCHEDULING AND ACCESSIBILITY
Even the best-designed system will need upkeep. That’s why accessibility and maintainability should be baked into the design, not treated as afterthoughts.
- Schedule routine inspections for wear parts like belts, scrapers, and rollers.
- Choose systems with accessible components, like slide-out idlers or hydraulic take-ups, to speed up maintenance and reduce downtime.
- Leverage remote monitoring (when available) to detect problems like belt misalignment or motor overheating before failure occurs.
The right maintenance strategy ensures minor issues don’t snowball into costly downtime.
CHALLENGES IN AGGREGATE ENVIRONMENTS AND HOW TO OVERCOME THEM
Even the most well-designed conveyors can struggle in harsh aggregate conditions. From constant abrasion to difficult terrain, these environments introduce challenges that demand thoughtful engineering and proactive upkeep.
Below are some of the most common issues and how to overcome them.
ABRASIVE MATERIALS
Sand, gravel, and crushed stone are relentless on equipment. These materials create constant friction and impact that can quickly degrade unprotected components. Over time, this leads to frayed belts, seized idlers, worn pulleys, and motor overloads, all of which increase downtime and repair costs.
To combat this, choosing the right transport method for aggregate is vital, and conveyor systems must be engineered with durability in mind. This includes:
- Abrasion-resistant belting, such as rubber compounds formulated specifically for aggregate or reinforced with fabric or steel.
- Impact beds and heavy-duty idlers at transfer points to absorb shock and protect belt integrity.
- Replaceable wear liners and skirting systems that can be serviced without major disassembly.
- Proper material flow control to reduce belt loading stress and limit localized wear.
Designing with abrasion in mind, rather than reacting to failure, means fewer unexpected shutdowns, longer equipment lifespan, and more predictable maintenance schedules.
UNEVEN TERRAIN
Pits, quarries, and stockyards are rarely uniform or level. Constant elevation changes, unstable ground, and shifting material piles can create alignment issues, impact loads, and increase wear on both the structure and components. In these conditions, a standard off-the-shelf conveyor may struggle to stay reliable or even operational.
Custom-engineered overland conveyors, designed with terrain variability in mind, offer a dependable solution. These systems incorporate:
- Modular support structures that can follow grade changes while maintaining belt alignment.
- Adjustable take-up units and drive configurations to maintain proper belt tension on uneven ground.
- Tailored belt layouts and pulley arrangements that suit the specific application help minimize spillage and reduce stress on the system.
West River Conveyors put this approach into action when designing a 1,000-foot overland system for Blue Water Industries’ sand operation in Cottageville, South Carolina.
The project required a conveyor capable of moving 300 tons of sand per hour across challenging terrain. To address this, West River designed a custom combination drive/take-up unit mounted on a single skid, eliminating the need for counterweights and simplifying installation.
The result was a system that delivered on stability, mobility, and reliability, ultimately saving the customer over $100,000 in installation and operational costs.
UNPLANNED DOWNTIME
Whether caused by worn components, misalignment, or sudden mechanical failure, conveyor downtime can bring your entire aggregate operation to a halt. The cost isn’t just measured in lost material movement—it’s lost productivity, delayed deliveries, and increased pressure on your crew.
Proactive strategies are key to preventing these costly disruptions. This includes:
- Scheduled inspections that focus on high-wear areas like tail pulleys, drive motors, and loading zones.
- Vibration and temperature monitoring sensors that can alert teams to misalignment, belt drift, or bearing failures before they lead to shutdown.
- Clear maintenance protocols and part inventories to reduce the time spent diagnosing and sourcing components during a breakdown.
Planning for service, rather than reacting to failure, gives teams more control over labor, safety, and equipment availability. It also protects your bottom line by extending the useful life of your system and avoiding emergency repairs that typically carry a premium.
FINDING THE IDEAL CONVEYOR FOR AGGREGATE HANDLING
Every aggregate operation is unique, but the goal is always the same: move more material, more efficiently, with less downtime and lower operating costs. From choosing abrasion-resistant components to designing for uneven terrain and planning proactive maintenance, the right conveyor system is key to consistent performance and operational efficiency.
At West River Conveyors, we specialize in custom-engineered solutions built specifically for the demands of sand, gravel, and crushed stone environments. Whether you need a new system or want to upgrade an existing one, our team can help you design the ideal conveyor for aggregate handling—one that delivers performance today and long-term value in the future.
Looking to improve your conveyor’s performance and reduce downtime?