Bulk Material Handling Conveyor Design Considerations
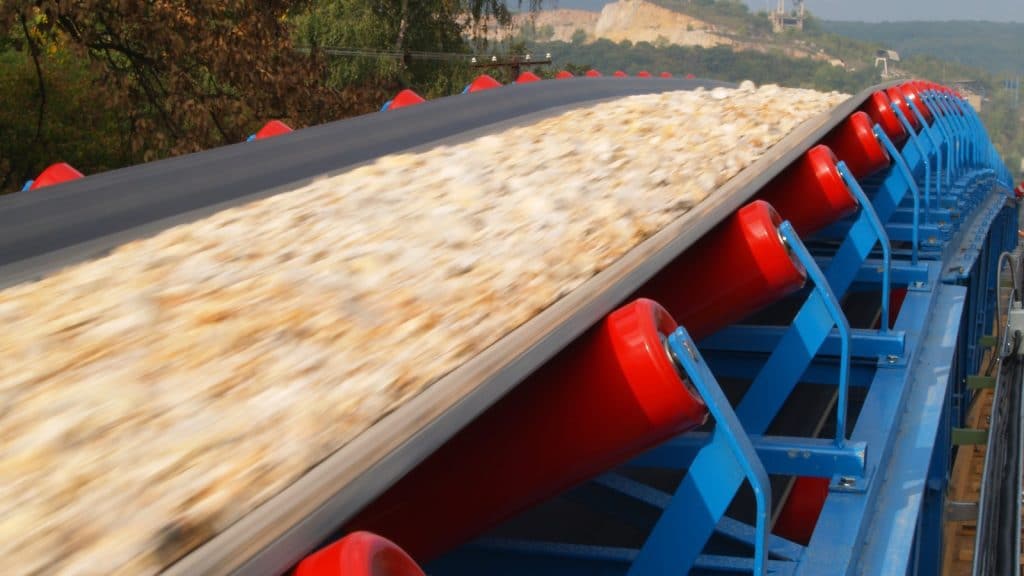
Material spills are wasteful and they create a cleanup problem, yet if your bulk material conveyor isn’t right for the job you’ll be dealing with them for a long time.
Designing a successful system poses a host of challenges, from weight to repose angle. Here’s some advice on what to consider next time you need to specify a bulk conveyor.
BULK CONVEYORS: BEGIN WITH THE END IN MIND
Bulk material handling conveyors move rock, construction aggregate, ore, or powder between two points, but they’re no less important than what happens at each end. The conveyor needs to integrate with both operations, whether that’s extraction, loading, or deposition. These processes define the material to be moved, the distance, and the rate. Only when those are clearly defined can work start on bulk material handling conveyor design.
DESIGNING A BULK CONVEYOR STARTS WITH UNDERSTANDING THE MATERIAL
Bulk density and repose angle are critical factors. Combined with the target tons per hour these let you size the conveyor in terms of width and feet per minute. These numbers aren’t enough though. You also need to understand the characteristics of the material. For example, is it:
- Wet or dry?
- Sticky/gummy or powdery?
- Sharp/abrasive?
- Primarily large lumps or a high proportion of fines?
The answers to these questions will dictate the type of belt needed, the idler roller design, and the need for belt scrapers. CEMA standards offer some guidance on material properties, but while that’s a starting point, consider getting your material analyzed before locking-in conveyor design details.
BELT SPEED VS. WIDTH
Dust generation and spillage are proportional to belt speed. While it may be tempting to run the belt as fast as possible to narrow it down and save money in operation, these costs may outweigh the savings. If there’s a way to run a wider belt slower, that’s probably a better option. (The cramped confines of mines change this calculus.)
PORTABILITY
Will you want to relocate the conveyor at some point? A conveyor is a significant investment, so it might be worth spending more to extend its useful life. Stacker and unloading conveyors are usually mobile, but this isn’t so true for all radial stacker conveyors and overland conveyors. They can be engineered to be portable though if this is specified at the start of the project.
DEFINE THE ENVIRONMENT
Most bulk material conveyors live outdoors, unless in a mine, but “environment” refers to more than just the weather conditions.
Weather matters, because wind can impose side loads while rain adds weight to uncovered material, but other factors to consider are:
- Distance
- Changes in elevation
- Terrain
- Dust exposure
- Availability of electricity
If it’s unloading or stacking, a bulk conveyor may only need to cover a few yards, but if it’s an overland conveyor it may run many miles.
An essential element of bulk material conveyor design is to define the distance it will work over and the amount of elevation change. These two factors, combined with knowledge of the material properties and tons per hour required, define the power needed in the drive system.
And note that the maximum gradient is determined largely by the repose angle of the material.
Designing an overland bulk conveyor requires knowledge of the terrain being traversed. There may be dips or gullies that need elevated sections of structure, and rivers or roads requiring changes in belt direction. If the belt is going into a dry location, dust may well be a problem that needs addressing during design.
Another point to consider is the availability of power. Many remote locations lack a source of AC power for the drive, in which case you need to plan for one or more generators.
REVIEW LOADING AND UNLOADING REQUIREMENTS
There are several things to consider at the point where the conveyor will be loaded. Material characteristics and target tonnage will determine belt loading and the chute or rockbox size. Modeling material flow will help with optimizing the design.
Another point is to determine the space available for the loading zone. The issue here is that belt life is better when there’s space to get it fully troughed before loading. Loading a troughed belt also reduces material spills, but the downside is that it increases the space needed.
At the unloading end material waterfalls off the belt. The shape of this waterfall is determined largely by belt speed and also the material properties, especially the relative proportions of large lumps and fines. To avoid spills and material segregation, review what will happen at unloading and design accordingly.
PROVIDE SUFFICIENT BELT CLEANING
Not cleaning the belt enough is a common design mistake. It leads to extra clean-up work and shorter belt life and adding cleaning later is expensive. The nature of the bulk material being conveyed will determine how much cleaning is needed – gummy or sticky material like asphalt will need more – and it’s better to do too much rather than too little.
DESIGN FOR SERVICE AND MAINTENANCE
Throughout the life of your bulk material conveyor, people will need access to various components. Idlers will need inspecting and possibly replacing. The same goes for scrapers. These maintenance activities should be considered during design.
Conveyor maintenance techs always have stories about piping and conduit runs preventing them from accessing parts of the conveyor. Ensure there’s room to open access doors and reach anything that may need attending to or you’ll increase maintenance costs dramatically.
ENGAGE WITH EXPERTS
Bulk material handling conveyor design is a complex business. There’s much that can go wrong and it takes experience to avoid the pitfalls.
This is why it pays to work with people who’ve done it before, like West River Conveyors. We have decades of conveyor design experience and can help you plan for and design a system that will meet your needs, now and in the long term.