Gravel Conveyance: Selecting Durable Conveyors for Heavy, Abrasive Material
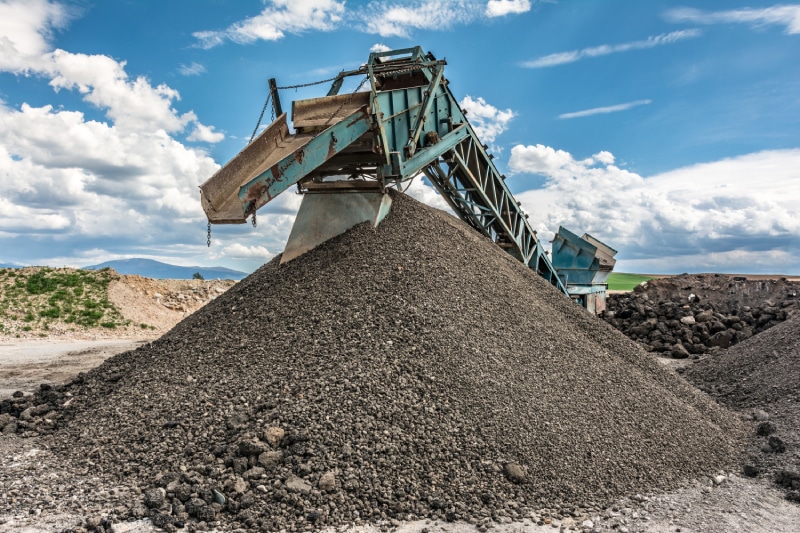
Gravel may seem simple at first glance, but in reality, its size, weight, and abrasiveness make it one of the most demanding materials to move. In mining and construction environments, choosing a conveyor for heavy material like gravel isn’t just a matter of preference—it’s essential for long-term performance, cost efficiency, and safety.
This blog will help you understand the material characteristics of gravel and how they impact equipment selection. We’ll walk through the key factors to consider when choosing a gravel conveyor, and why the right combination of components can mean the difference between reliable operation and recurring breakdowns.
UNDERSTANDING GRAVEL: A HEAVY, ABRASIVE CHALLENGE
Gravel presents a tough mix of challenges for any conveyor system:
- Bulk density and particle size: Gravel is heavy and coarse, often exceeding 100 lbs per cubic foot. This requires systems that can support and transport materials without excessive strain or sagging.
- Abrasive materials: Gravel’s jagged edges accelerate wear on belts, pulleys, and structural components, particularly in high-friction zones like loading areas and transfer points.
- High-volume expectations: Systems moving gravel often need to hit throughput targets of hundreds of tons per hour, making efficiency non-negotiable.
In addition to its physical demands, gravel-handling operations often involve harsh conditions: long distances, variable terrain, high drop heights, and exposure to the elements. From stationary overland conveyors to radial stackers and portable transfer units, the type of conveyor you choose must be engineered to deliver consistent performance despite these variables.
Because of these challenges, gravel-handling systems require more than an off-the-shelf solution. They demand a conveyor built to handle punishing loads, resist wear, and perform reliably under high-stress conditions—day in and day out.
KEY FACTORS IN CHOOSING A CONVEYOR FOR ABRASIVE MATERIAL
To meet production goals and reduce downtime, it’s critical to choose components specifically designed to withstand gravel’s impact. System design must consider everything from bulk density to material flow rate—key factors that can make or break performance.
REINFORCED CONVEYOR BELTS
Not all conveyor belts are created equal. For gravel, reinforced belts with high-tensile strength and abrasion-resistant covers are essential. Look for options rated for sharp, heavy loads and designed to reduce wear even under constant use.
HEAVY-DUTY PULLEYS AND SHAFTING
Head, tail, and snub pulleys must be sized and lagged appropriately to manage belt tension and direction changes. Using undersized or unlagged pulleys can result in premature belt failure or alignment issues.
IMPACT BEDS AND WEAR LINERS
Loading zones bear the brunt of material drop. Installing impact beds and wear liners protects your system structure, reduces vibration, and helps prevent damage to belts and idlers. These are especially important if you’re dealing with variable particle size or high drop heights.
PROPERLY SIZED DRIVE SYSTEMS
Gravel requires powerful, efficient drive systems. Motors and gearboxes must be chosen based on load requirements, system layout, and material transport rates. A mismatch here can lead to energy inefficiency or even mechanical failure.
SKIRTING, SCRAPERS, AND CONTAINMENT
To prevent material spillage and minimize dust, look for systems with effective containment features. Skirting and scrapers keep gravel on the belt and reduce carryback, a common cause of wear and maintenance headaches.
THE RISKS OF IMPROPER COMPONENT SELECTION
When conveyors are not built with gravel in mind, issues can show up fast, and they’re often the same conveyor issues seen across all bulk handling environments. From excessive belt wear to material loss and system breakdowns, improper component selection can lead to safety risks, downtime, and expensive repairs, many of which can be avoided through routine maintenance practices that extend the life of your conveyor system.
- Premature wear on belts, idlers, and bearings
- Material spillage due to poor containment or loading alignment
- Belt tracking issues and misalignment
- Motor strain and failures due to improper drive sizing
- Downtime and unplanned maintenance that throw off production schedules
These risks aren’t just frustrating—they’re expensive. Choosing a conveyor for heavy material that isn’t built to handle the demands of gravel will cost more in the long run.
WHY PARTNER WITH WEST RIVER CONVEYORS
At West River Conveyors, we specialize in designing and manufacturing conveyor systems for the toughest jobs, including gravel. Our engineers work closely with mining and construction operations to build heavy-duty systems tailored to each site’s unique requirements. We offer:
- Custom overland and transfer conveyor designs for gravel and similar bulk material handling applications.
- Components selected based on your material characteristics, layout, and production goals.
- High-performance parts like impact beds, dust containment systems, wear liners, and belt conveyor structures that hold up in real-world conditions.
- Long-term cost savings by helping you move materials more efficiently and with fewer repairs.
We understand that no two job sites are alike. That’s why our systems are engineered for your specific environment, from steep inclines and remote locations to tight spaces and high-volume demands. Whether you’re transporting sharp-edged gravel over long distances or need equipment that can be repositioned quickly, we deliver rugged, cost-effective solutions that perform under pressure.
You’re not just buying a conveyor—you’re gaining a partner focused on long-term uptime, easy maintenance, and better results from day one.
CHOOSE A GRAVEL CONVEYOR BUILT TO LAST
Gravel is a challenging material, but with the right equipment in place, it becomes a manageable part of your operation. The right conveyor system can reduce maintenance needs, extend equipment lifespan, and help you stay on track with production goals.
Here’s what to consider moving forward:
- Review your site layout and key loading zones to identify where added protection or reinforcement may be needed.
- Evaluate throughput demands to ensure your system is sized for efficiency and longevity.
- Consult with a conveyor specialist who can help match component specifications to your specific material and environment.
West River Conveyors builds systems that are engineered for the realities of sand, gravel, and aggregate operations. From belt strength to wear protection and custom layouts, we design with performance and long-term reliability in mind.