Top 7 Safety Features Your Conveyor Should Have
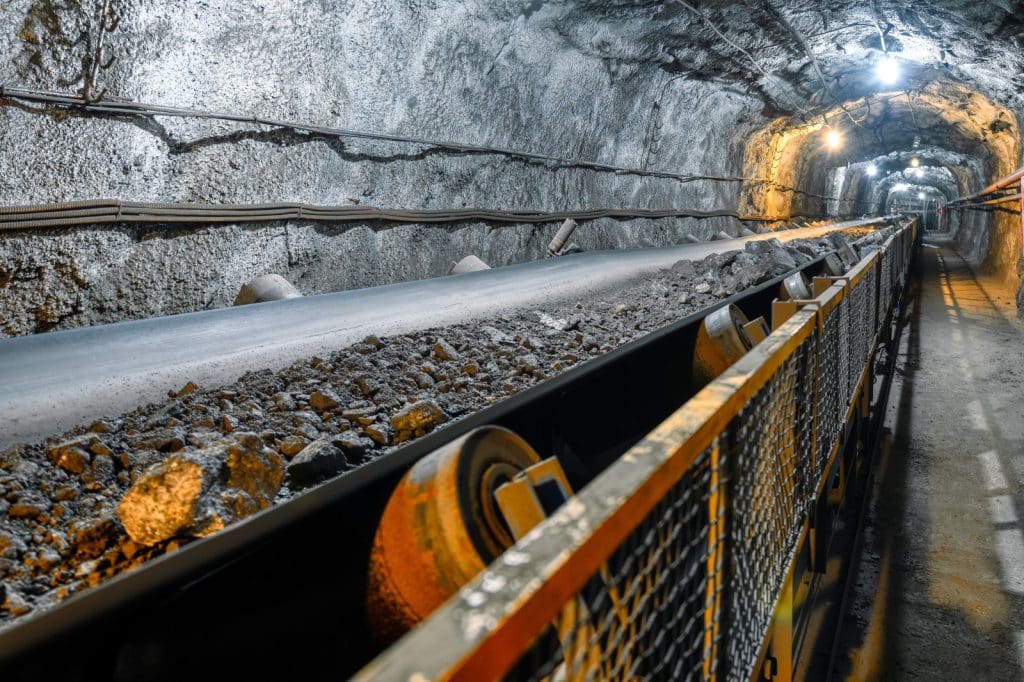
Adhering to complex OSHA mining conveyor safety regulations can be an ongoing challenge. There are many moving parts and areas where accidents could occur. However, failure to comply poses serious legal, financial, and reputational risks.
Adding key safety features to your conveyor systems can mitigate hazards and ensure your operations conform to regulatory rules. Read on to learn more about OSHA conveyor safety and compliance.
IMPORTANCE OF CONVEYOR SAFETY IN MINING
Mining conveyors pose inherent safety risks due to multiple moving parts, heavy loads, and continuous operation. Well-implemented safety components and protocols ensure compliance and foster a safe working environment.
Here are the top seven mining conveyor safety features you should consider:
1. GUARDING
Proper conveyor guarding prevents access to moving parts and hazardous areas. It is an effective measure to protect operators from injuries caused by moving components. The impact of guarding on worker safety is significant, as it directly reduces the risk of accidents and injuries.
OSHA REGULATIONS ON GUARDING
OSHA’s General Industry Standard, specifically 29 CFR 1910.219, underlines the requirements for guarding machinery. This standard directly applies to conveyor systems, mandating guards to protect workers from moving parts, pinch points, and other potential hazards.
2. EMERGENCY SHUT-OFF BUTTONS
Emergency shut-off buttons or pull cords are vital for immediate response in hazardous situations. These controls allow for the quick shutdown of the conveyor, thereby minimizing the risk of accidents and enhancing safety. Quick and unimpeded access to emergency controls is essential for effective emergency response.
OSHA STANDARDS FOR EMERGENCY CONTROLS
According to OSHA’s Conveyor Standard, 29 CFR 1910.261, conveyors must have easily accessible emergency stop devices. This regulation ensures workers can quickly halt conveyor operations in an emergency.
3. START-UP WARNING SYSTEMS
Start-up warning systems allow operators and nearby workers sufficient time to clear the area before the conveyor starts. These systems provide audible or visible signals that enhance safety by alerting workers allowing them to move to safe locations.
OSHA AND START-UP WARNINGS
OSHA guidelines related to conveyor warning systems are an integral part of safety protocols. These guidelines ensure that workers have adequate warning before the conveyor operation commences. This early warning system helps to reduce accident risks significantly.
4. SCHEDULED MAINTENANCE
Performing regular maintenance is vital for spotting safety issues before they worsen. Scheduled inspections and upkeep help find hazards like worn parts, loose components, or faulty equipment. This allows for prompt fixes and helps sustain the conveyor’s safety and integrity.
OSHA’S PERSPECTIVE ON MAINTENANCE
OSHA emphasizes the importance of regular inspections and maintenance of conveyors through its Conveyor Standard, 29 CFR 1910.261. This standard mandates periodic checks to ensure the safe operation of conveyors.
Additionally, following the Lockout/Tagout (LOTO) standard (29 CFR 1910.147) is vital during maintenance to safeguard workers. LOTO prevents unexpected startups that could endanger them.
5. PERSONAL PROTECTIVE EQUIPMENT (PPE)
Wearing proper personal protective equipment (PPE) directly safeguards against many hazards while safeguarding worker health and safety. Required PPE varies by work environment but can include safety glasses, gloves, and hearing protection.
OSHA REGULATIONS ON PPE
The OSHA standard for PPE, 29 CFR 1910.132, mandates employers to assess workplace hazards and provide appropriate personal protective equipment. This standard is crucial for ensuring that employees working with conveyors are adequately protected from potential risks.
6. SENSOR AND ALARMS
Sensors and alarms play a critical role in detecting abnormalities in the conveyor system. They can identify issues like jammed materials, excessive loads, or equipment malfunctions. These warning systems are crucial for preventing shutdowns and accidents, enhancing the overall safety of the conveyor system.
OSHA GUIDELINES FOR TECHNOLOGICAL SAFETY MEASURES
OSHA regulations on using technology for safety in conveyor systems are integral to modern safety protocols. They ensure conveyors have the latest safety technology to detect and respond promptly to potential hazards. Applicable regulations can include:
29 CFR 1926.555 – Conveyors: This regulation covers the safety requirements for various types of conveyors, including using technology to enhance safety.
29 CFR 1910.147 – Control of Hazardous Energy (Lockout/Tagout): While not specific to conveyors, it pertains to machinery safety, which can include safety technology on conveyors.
29 CFR 1910.212 – General Requirements for Guarding of Machinery and Mechanical Power Transmission Apparatus: This regulation addresses guarding and safety measures for machinery, which may involve conveyor systems and their safety technology.
7. PROPER STICKERS AND WARNING LABELS
Stickers and warning labels are essential for conveyor safety. They offer clear, visible instructions and warnings to workers. These labels inform about potential hazards and safety procedures associated with operating or working near conveyors. They serve as reminders for the use of necessary protective gear and guide on safe machinery operation.
OSHA GUIDELINES FOR STICKERS AND WARNING LABELS
Under OSHA’s General Requirements (29 CFR 1910.22), maintaining a safe and orderly workplace is crucial. This includes the use of stickers and warning labels around conveyors. Employees should place these strategically so that they’re easily seen and understood.
WEST RIVER CONVEYORS SAFETY FEATURES
Our conveyors integrate all the safety components outlined above. If you require any of these mechanisms, you can have us install them directly. Our experienced team fabricates a wide range of customizable guarding options in-house to meet all safety standards.
Our expert fabricators can integrate these safety features into new or existing systems to guarantee compatibility with your West River Conveyors equipment. We comply with OSHA regulations and verify that all necessary protective mechanisms are included on our conveyors.
For instance:
- Guarding complies with the Mechanical Power-Transmission Apparatus standard (29 CFR 1910.219)
- Emergency shut-off buttons adhere to the Conveyor Standard (29 CFR 1910.261)
- Regular inspections and maintenance follow the guidelines of the Conveyor Standard (29 CFR 1910.261) and the Lockout/Tagout standard (29 CFR 1910.147)
- Personal Protective Equipment provided aligns with the OSHA PPE standard (29 CFR 1910.132)
GET EXPERT CONVEYOR SAFETY GUIDANCE
Implementing the above safety features will help create an efficient, productive, and sustainable working environment. Worker morale will also improve as the company takes the necessary steps to ensure their health and well-being.
At West River Conveyors, we have over 40 years of experience building high-performance and long-lasting mining conveyors for various industries. We can help you navigate through the often-complex maze of conveyor safety regulations and requirements.
We invite you to click below to learn more about our innovative conveyor safety features.